以下是根据全面质量管理(TQM)理论解决生产流程优化问题的高考实战思路与步骤,结合理论要点与实际案例分析:
一、理论框架与核心概念
全面质量管理(TQM)强调以客户为中心、全员参与、过程控制和持续改进。其核心工具包括PDCA循环、5M1E分析法(人、机、料、法、环、测)、标准化流程和数据驱动决策等。
二、生产流程优化解题步骤
1. 识别问题与目标设定
问题定位:通过数据分析或客户反馈,明确生产流程中的关键问题(如效率低、次品率高、成本浪费等)。例如,某工厂因设备故障导致生产线停滞频繁,次品率高达15%。目标量化:设定可衡量的优化目标,如“次品率降至5%以下”或“生产效率提升20%”。2. 分析根本原因(5M1E法)
人员(Man):操作技能不足或质量意识薄弱。设备(Machine):设备老化、维护不足。材料(Material):原材料质量不稳定。方法(Method):工艺流程不科学或缺乏标准化。环境(Environment):生产环境温湿度不达标。测量(Measurement):检测工具精度不足或标准不统一。3. 制定改进方案
PDCA循环应用:计划(Plan):针对问题根源制定措施,如引入设备定期维护计划、员工培训方案。执行(Do):实施改进措施,如更新设备、优化工艺参数。检查(Check):监控改进效果,统计次品率、生产效率等数据。处理(Act):若有效则标准化流程,若无效则重新分析。标准化流程:建立标准作业程序(SOP),确保每个环节可控。例如,麦当劳通过统一操作手册实现全球分店质量一致。4. 全员参与与培训
通过质量小组(QCC)或提案制度激励员工参与改进。例如,丰田的“自働化”理念要求每个员工发现异常时立即停机并解决问题。5. 数据驱动与持续改进
利用统计过程控制(SPC)监控生产数据,通过控制图识别异常波动。定期复盘,如每月召开质量会议分析问题并优化流程。三、经典案例分析
案例1:丰田精益生产
问题:生产浪费严重,效率低下。TQM应用:消除七大浪费(过量生产、等待、运输等)。通过“看板管理”实现准时化生产(JIT)。结果:生产效率提升30%,库存成本降低50%。案例2:星巴克供应链优化
问题:原材料质量波动影响咖啡口感。TQM应用:与供应商建立长期合作,制定统一质量标准。使用HACCP系统监控食品安全。结果:客户满意度提升20%。四、答题要点与注意事项
1. 逻辑清晰:按“问题识别→原因分析→方案制定→实施验证→标准化”顺序展开。
2. 结合工具:明确提到TQM工具(如PDCA、5M1E、SPC)并解释其在案例中的应用。
3. 数据支撑:量化目标和结果(如“次品率从15%降至5%”)。
4. 案例引用:优先选择制造业标杆案例(如丰田、通用电气)以增强说服力。
五、模拟试题示例
题目:某电子厂组装线次品率高,请运用TQM理论提出优化方案。
参考答案:
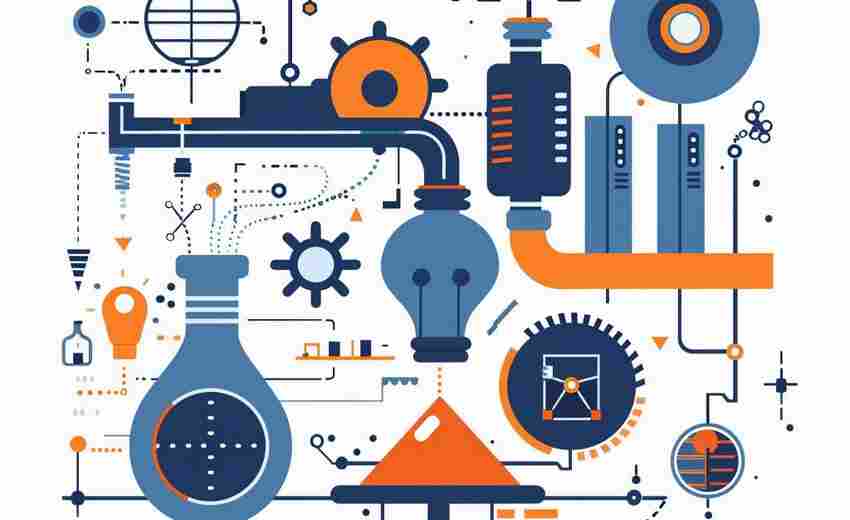
1. 问题定位:次品率高达12%,主要缺陷为焊接不良和部件错装。
2. 5M1E分析:
人员:新员工培训不足;设备:焊机温度设定偏差;方法:缺乏防错装设计。3. 改进措施:
引入自动焊机并定期校准温度;设计防错夹具(Poka-Yoke);建立员工技能考核制度。4. 效果验证:PDCA循环后次品率降至3%。
通过以上框架,考生可将TQM理论与实际问题结合,形成结构化、数据驱动的解决方案,符合高考实战中“理论联系实际”的考核要求。
推荐文章
动物医学与兽医的区别是什么
2024-10-28长丰的考试科目有哪些
2024-12-11教育部教学质量国家标准如何影响高校招生竞争力
2025-03-17兽医学专业需要哪些基础学科知识储备
2025-04-02西南大学历史学专业课程如何助力高考历史复习
2025-03-30家庭经济与消费的研究重点是什么
2025-01-11高考志愿填报中如何处理家庭期望
2024-11-24高三学生如何通过时间管理提升弱科成绩
2025-04-17高考分数线是什么
2025-01-23高考 估分(高考估分选大学 在线)
2023-11-23